Why Normal Tank Welding Inspection is Crucial for Architectural Honesty
Why Normal Tank Welding Inspection is Crucial for Architectural Honesty
Blog Article
The Crucial Duty of Container Welding Examination in Ensuring Structural Honesty and Safety And Security Conformity in Industrial Applications
In the world of industrial applications, storage tank welding inspection arises as a pivotal aspect in guarding structural integrity and making sure compliance with security laws. Utilizing a mix of strategies such as visual analyses and advanced testing techniques, these inspections serve to recognize and mitigate prospective imperfections before they intensify right into substantial risks.
Value of Container Welding Evaluation
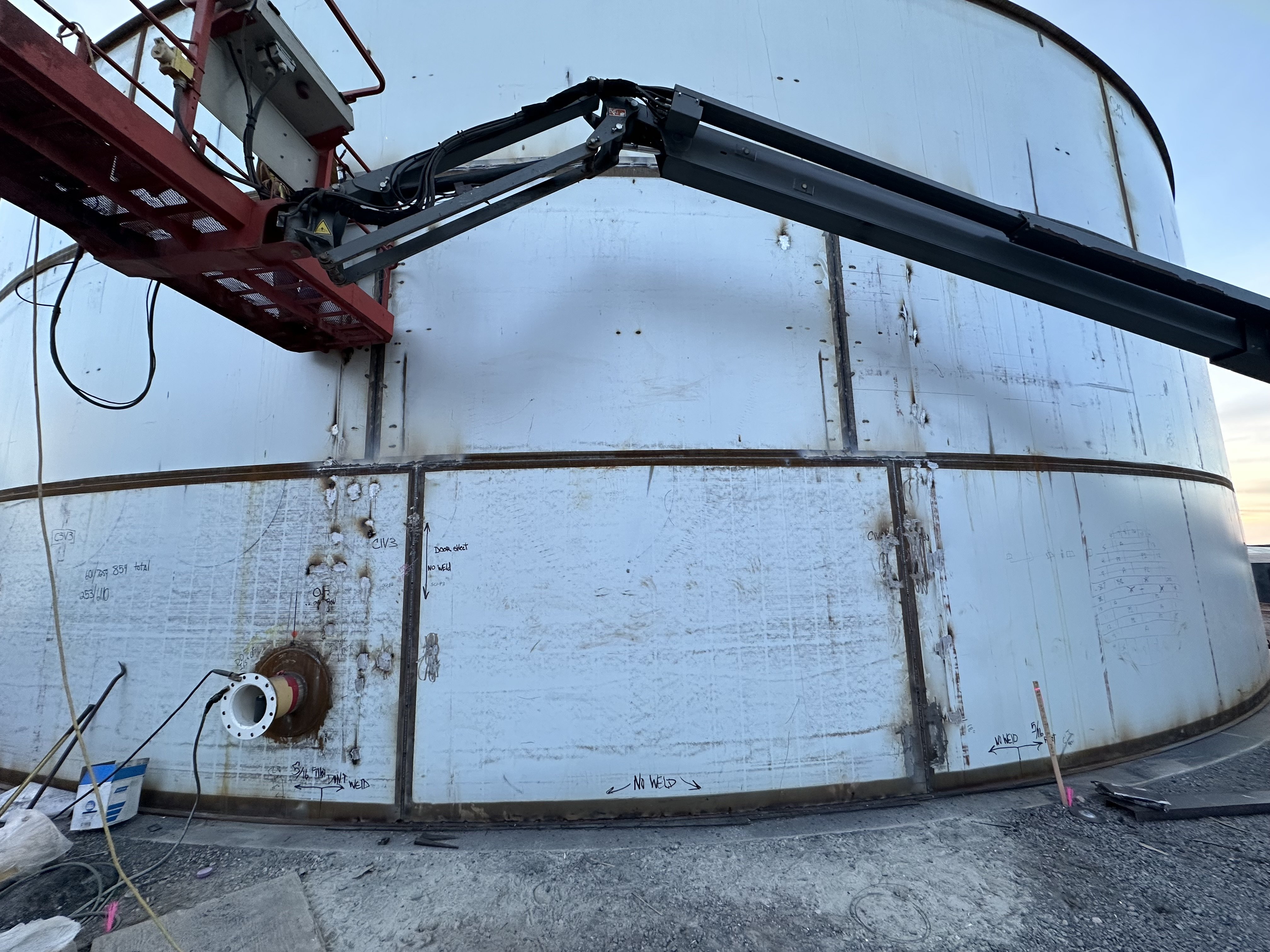
Guaranteeing conformity with sector criteria and laws is another significant aspect of storage tank welding assessment. Regulative bodies mandate rigorous standards for the building and construction and upkeep of tank, and extensive assessments assist companies abide by these demands. Non-compliance can lead to serious charges, consisting of penalties and closures, additionally stressing the need for rigorous examination methods.
In addition, storage tank welding evaluation plays an essential duty in preserving operational performance. In summary, the importance of storage tank welding evaluation exists in its capability to safeguard public wellness, safeguard the setting, and make sure compliance with regulative frameworks.
Key Assessment Strategies
Effective tank welding evaluation counts on a range of key methods that make certain comprehensive analysis of weld quality and structural honesty. Among the most common strategies are visual evaluation, ultrasonic screening, radiographic screening, and magnetic particle testing - Tank Welding Inspection. Each approach offers distinct benefits in analyzing different aspects of the weld
Visual assessment acts as the first line of defense, enabling assessors to recognize surface area defects, irregularities, or variances in the weld grain. Ultrasonic screening uses high-frequency acoustic waves to spot interior problems, such as splits or gaps, providing a comprehensive evaluation of weld stability. This technique is especially efficient in discovering problems that might not show up externally.
Radiographic screening makes use of X-rays or gamma rays to generate photos of the welds, disclosing inner stoppages and providing a permanent document for future referral. This strategy is very reliable for essential applications where the threat of failing have to be decreased.
Last but not least, magnetic fragment screening is utilized to recognize surface area and near-surface flaws in ferromagnetic products. By applying magnetic fields and fine iron particles, assessors can determine interruptions that may jeopardize the structural integrity of the storage tank. Together, these techniques create a durable structure for ensuring top notch welds in commercial applications.
Compliance With Safety Specifications
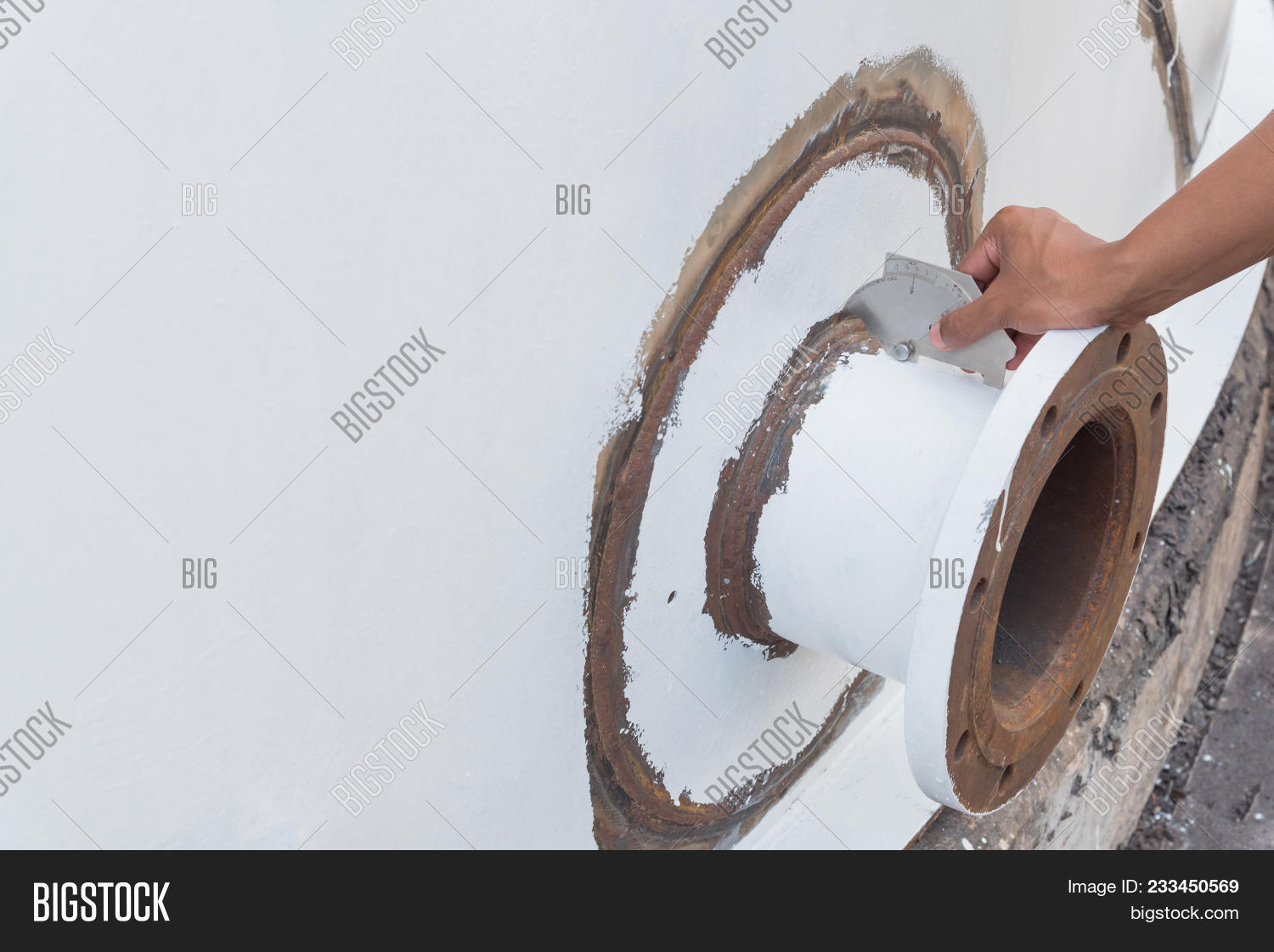
Normal assessments play a critical duty in making sure compliance by recognizing potential failings or variances from prescribed requirements. Inspectors are educated to evaluate weld top quality, verify product specifications, and evaluate the general structural integrity of containers. Their knowledge is important in guaranteeing that welding processes meet the required safety criteria.
Furthermore, conformity with safety requirements not just protects employees yet also safeguards the setting from potential risks such as leakages or catastrophic failures. Organizations that prioritize security conformity are better positioned to alleviate risks, enhance functional performance, and foster a culture of safety and security within their labor force. In summary, preserving strenuous conformity with safety requirements is crucial for the effective operation of storage tank welding tasks in commercial setups.
Benefits of Regular Evaluations
Normal examinations are integral to maintaining the structural stability and safety and security of bonded tanks. These inspections offer a methodical technique to recognizing possible issues or weaknesses in the welds, ensuring that any kind of issues are addressed before they escalate into significant failures. By conducting Check This Out regular assessments, organizations can discover rust, tiredness, and other types of wear and tear that may jeopardize tank performance.
Additionally, consistent assessments contribute to conformity with market policies and requirements. Sticking to these guidelines not just minimizes lawful dangers however likewise enhances the company's online reputation for safety and reliability. Normal inspections promote a proactive safety and security culture, urging workers to acknowledge and prioritize the importance of tools stability.
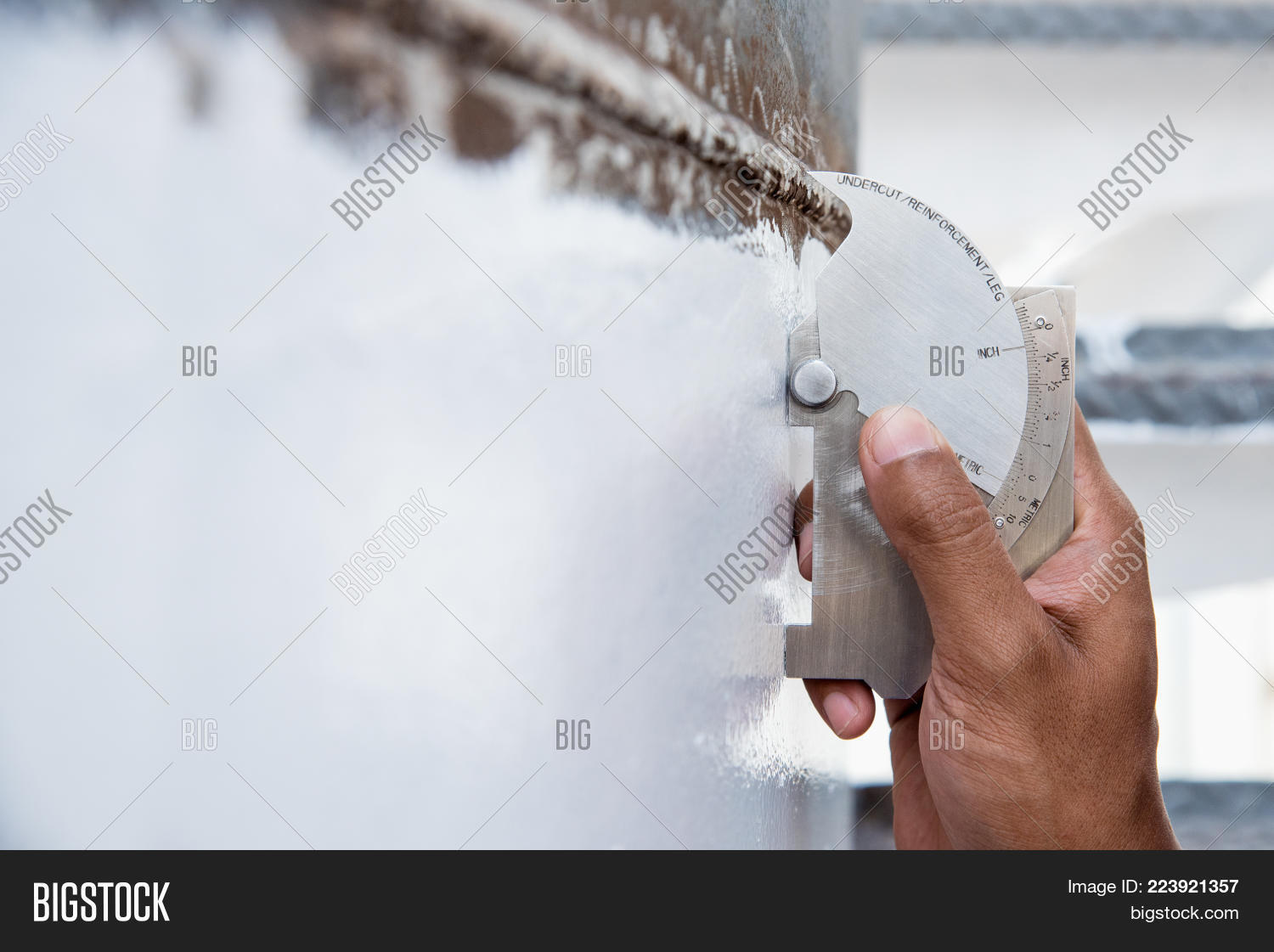
Situation Studies and Real-World Applications
Instance studies and real-world applications show the substantial impact of efficient tank welding evaluation techniques. Following the application of strenuous welding inspection procedures, consisting of aesthetic and ultrasonic testing, the facility determined critical defects in weld joints that can have led to catastrophic failures.
Likewise, a water therapy plant applied an extensive assessment program for its container welding procedures - Tank Welding Inspection. By incorporating non-destructive testing techniques, the plant had the ability to identify early signs of corrosion and tiredness in weld joints. This prompt treatment expanded the life-span of the containers and ensured compliance with safety policies, therefore securing public wellness
These study emphasize the importance of regular and systematic tank welding inspections. By prioritizing these practices, industries can reduce risks, enhance structural integrity, and make sure conformity with security requirements, eventually resulting in improved operational efficiency and reduced responsibilities.

Conclusion
In verdict, container welding examination is a crucial component of keeping structural stability and safety in commercial applications. Using different examination methods ensures very early detection of prospective imperfections, thus protecting against devastating failings.
Report this page